Innovative retort furnaces for metal powder processing
Electron is a specialized manufacturer of advanced controlled atmosphere furnaces and a strategic collaborating partner for advanced metal powder processing activities. Electrons expertise lies in supplying custom built thermal processing equipment for companies that produce and further refine metal powders, particularly high-tech metals such as Titanium, Zirconium, Tantalum and Niobium. Our systems are designed to handle virtually all metals, tailored and customized to the specifications and unique process of each individual customer.

Challenges in metal powder processing
In the dynamic world of metal powder processing, it very often can be a challenging procedure to seamlessly integrate knowledge gained from small-scale laboratory type experiments into large-scale production processes for the efficient manufacturing of high-quality metal powders.
The lack of in-depth production based process knowledge can be particularly evident when scaling up powder processes, with the main stumbling block being maintaining high product quality along with efficient product yield outputs.
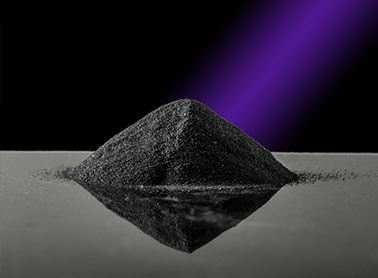

Innovative partner for efficient production
At Electron, we understand the complexity of these challenges and offer customized solutions.
Our expertise is in optimally translating processes from laboratory scale to demonstration phase and to full-scale production.
This field proven collaborative approach leads to system designs and installations offering the highest levels of processing quality, optimized performance, maximum operational productivity and further offering low operating costs and energy consumption.
High-quality retort furnace systems for efficient production
Electron – Your partner for high-quality thermal processing plants and process optimization
Hydriding process
Within the hydriding process and where Hydrogen is a critical processing parameter, Electrons advanced furnaces provide optimal temperature and Hydrogen process gas control and under the supervision of multiple in situ safety control protocols.
The superior processing equipment technologies ensure uniform Hydrogen process integration resulting in high-grade consistently reliable product output yields.
Electron systems meet the highest safety standards for hydrogen processing.
Deoxygenation process
For deoxygenation processing, Electron offers field proven methods and expertise to successfully remove Oxygen from materials and as part of a fully integrated process.
Customer-specific processes with reactive materials such as Magnesium are carefully managed and controlled to result in precise, uniform and maximum deoxygenation parameter levels. This contributes to high-quality metal powders with the lowest possible (residual) Oxygen content remaining.
Debinding & sintering
The debinding & sintering process requires high-quality structure formation. Electrons furnace technology through optimized pyrolysis and sintering process methods readily creates open foam structures for optimal powder generation.
Leveraging our proven technology expertise for consistent results in structure and process quality is the smart way to achieve long term operational and profitable results.
Dehydriding process
Safety and efficiency are central to the dehydriding process.
Electron’s furnace systems accurately manage the removal of Hydrogen from metal powder at high operational temperatures and under high vacuum processing conditions.
Our innovative dehydriding systems offer the perfect balance between speed, safety and quality of all processing steps.
System specifications
Baseline specifications of our retort furnace installations:
- Retort diameter: 500, 750, 1,000, 1,250 and 1,500 mm (19.6”, 29.5”, 39.3”, 49.2” and 59”)
- Working height: 1,000, 1,500, 2000, 2500 and 3,000 mm (39.3”, 59”, 78.7”, 98.4” and 118.1”)
- Temperature: up to 1,200°C (2,192°F)
- Ultimate vacuum: <1x10-4 mbar (<7.5x10-5 Torr)
- Max. positive pressure: 500 mbar (375 Torr)
Customized installations
At Electron, we understand that every process and application is unique. That is why we design and make customized thermal processing systems, fully aligned to specific customer needs.
Our approach is to always be flexible and focused on providing solutions that are not only meeting the requirements, but that will also service customers long term activities.
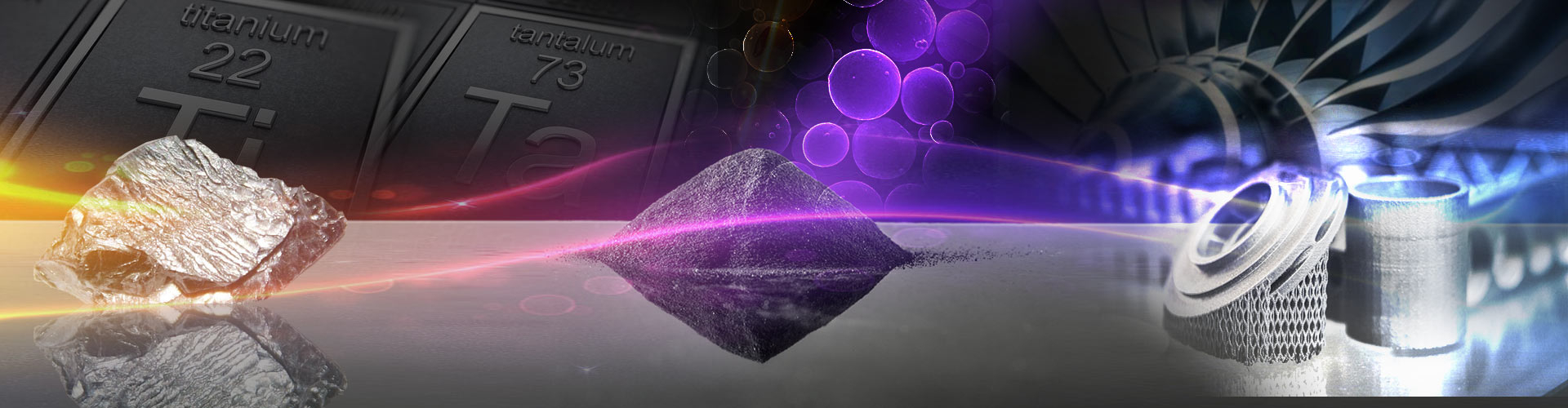
Why choose Electron?
As a leading equipment supplier, Electron offers a unique product & services portfolio inclusive of:
In-depth process knowledge
Electron intimately understands the challenges that will arise when a customer is upgrading or replacing existing thermal processing system technologies as well as scaling up laboratory development to fully-fledged production operations. Our team can provide the expertise needed to effectively stage-gate and manage this demanding sequence of events and not being content to just be an equipment supplier. We are not just a supplier. Electron performs as your collaborative knowledge partner, focused upon smoothly guiding businesses through to a successful process outcome.
Our in-depth process knowledge goes beyond just technical aspects; it also includes the strategic decisions essential for a successful scale-up. Process development is essential in the journey to large-scale production. Our experienced engineers are there to provide support in both advanced analysis techniques and further performing R&D testing and process demonstration trials.
Electron has in-house R&D facilities for process validation. This offers a unique opportunity to test production cycle feasibility on a scale comparable to a production-sized unit.
Consistent performance and built-in verification
In a world where precision is essential, Electron systems stand out by achieving exceptional temperature and flow uniformity, under all operating conditions. Built-in verification capabilities and extensive data logging routines support documented processes and with historical trending for ongoing data analysis. This fully ensures that our furnace installations readily comply with the latest AMS2750 Pyrometry standards.
Safety with reactive materials and process gasses
Manufacturing processes can involve complex and reactive materials along with explosive and toxic process gasses.
Electron furnaces are designed to the highest standards of safety engineering, when working with highly reactive substances such as Hydrochloric acid gas and pure Magnesium and with explosive gas including Hydrogen.
Achieve consistent quality, efficient production and lower TCO with Electron’s retort furnaces. Expertise, customization & hot-wall furnace design