Ultra-high temperature tube furnaces
Electron is a manufacturer of ultra-high temperature furnace systems, specializing in cutting-edge heating elements, designed for up to 2200°C. A process-first approach has resulted in our hot-wall furnace design that ensures optimal performance in applications such as Silicon Carbide wafer processing.
We have experience with both laboratory and production environments, where extreme conditions often require careful consideration of all components. We design custom UHT tube furnaces fully aligned to specific customer needs.
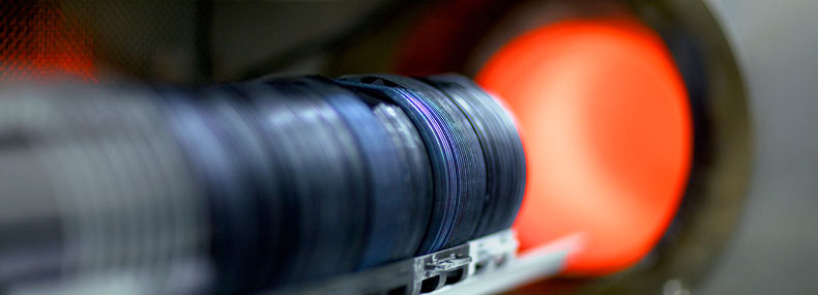
Ultra-high temperature furnaces for SiC processing
In the semiconductor industry's evolution, Silicon Carbide (SiC) has become a cornerstone, driving high-power applications.
Electron's ultra-high temperature tube furnaces excel in SiC wafer processing, providing a crucial environment for achieving and maintaining the extreme temperatures essential for high-quality Silicon Carbide processing.
With temperatures up to 2200°C, Electron's SiC furnaces, designed for 4, 6 or 8 inch wafers, are the best choice for SiC wafer processing equipment.
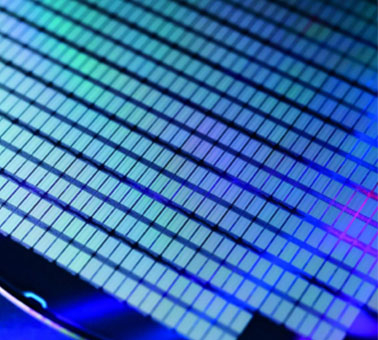
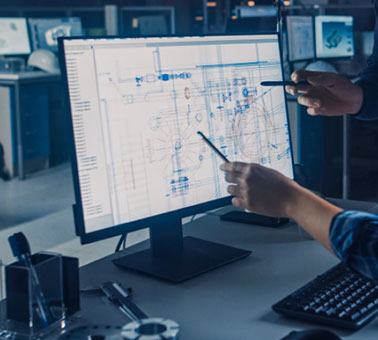
Process-first furnace design
Electron has a process-first approach, acknowledging the unique demands of each step. In processes like SiC activation, existing diffusion furnaces lack the required heat for efficient operation in any reasonable timeframe.
At Electron, we've embraced a new design approach, where temperature considerations are intrinsic. Furnaces are built around specific processes, ensuring that all required features are seamlessly integrated into the system. Our purpose-built furnaces excel in accommodating even the most exotic process conditions, guaranteeing unparalleled performance.
Versatile UHT tube furnace processes
Electron’s ultra-high temperature furnaces are designed for a variety of processes. From Post Oxidation Annealing (POA) in NO, N₂O or NH₃ atmospheres to Wet Oxidation, high-temperature H₂ substrate pre-treatment and Post implantation annealing.
Whether optimizing trenches for H₂ annealing or annealing with GaN or AlN, our ultra-high temperature furnaces provide precise control and reliability for diverse advanced applications.
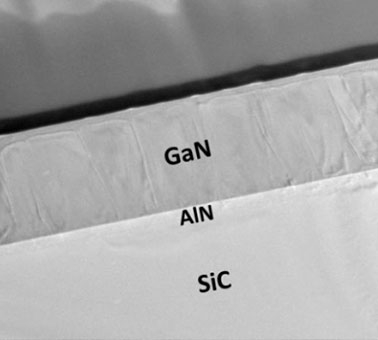
Need help selecting an ultra-high temperature furnace?
Discover how Electron's SiC tube furnaces can optimize your processes. Benefit from our tailored solutions and expert guidance.
SiC oxidation process
Ultra-high temperature oxidation of Silicon Carbide wafers is typically performed under controlled partial pressure of non-oxidizing gases—Nitrogen, Argon or Hydrogen. Utilizing O₂, NO, H₂O, CO and CO₂ as oxidizers, our furnaces for SiC wafer processing precisely manage temperature and partial pressures, ensuring optimal Silicon Oxide growth on the wafer surface.
SiC+ 3/2 O₂ ⇔ SiO₂ + CO
SiC+ 3 H₂O ⇔ SiO₂ + 3 H₂ + CO
SiC+ 3CO₂ ⇔ SiO₂ + 4 CO
Doping process & CVD
Elevate Silicon Carbide wafer properties with Electron's UHT furnaces, where meticulous doping processes change the electrical properties of the material.
While ion implantation is a common method, Electron explores alternative techniques within its equipment, like CVD where reactive gas deposits material on the wafer surface. Materials such as Aluminium, Boron, Nitrogen and Phosphorus facilitate diverse doping possibilities.
SiC activation process
Post-implantation annealing eliminates vacancy defects in Silicon Carbide wafers, driving solid-state diffusion. As temperature rises, the process accelerates exponentially, activating dopants.
This activation, also known as doping activation, unleashes free electrons, enhancing semiconductor properties.
UHT annealing
Beyond defect reduction, annealing processes enhance electrical properties of the wafer and refine trench edges, minimizing current crowding after etching.
Tailored for diverse materials, our UHT annealing furnaces extend benefits beyond Silicon Carbide, accommodating various compounds like Gallium Nitride (GaN) and Aluminium Nitride (AlN), broadening their applicability in semiconductor and other material processing.
Key features
Electron’s UHT furnaces boast advanced technical specifications for unmatched performance and precision in ultra-high temperature applications.
- Designed for wafer size up to 8"
- Versatile operation in high vacuum, atmospheric and overpressure conditions
- Controlled atmosphere processing: O₂, N₂O, NO, N₂, Ar, H₂ and H₂O
- Achieve unprecedented temperatures with an operational capability up to 2200°C
- Heating rates up to 100°C/min
Customized SiC tube furnaces
At Electron, we recognize that every process is unique, especially in SiC wafer processing. That's why we design custom ultra-high temperature UHT furnace systems, precisely tailored to meet individual customer requirements.
Our flexible approach, tailored for research, end-users and OEMs, ensures that every aspect is adapted or custom-specified to enhance the efficiency and effectiveness of SiC wafer processing and other ultra-high-temperature applications.
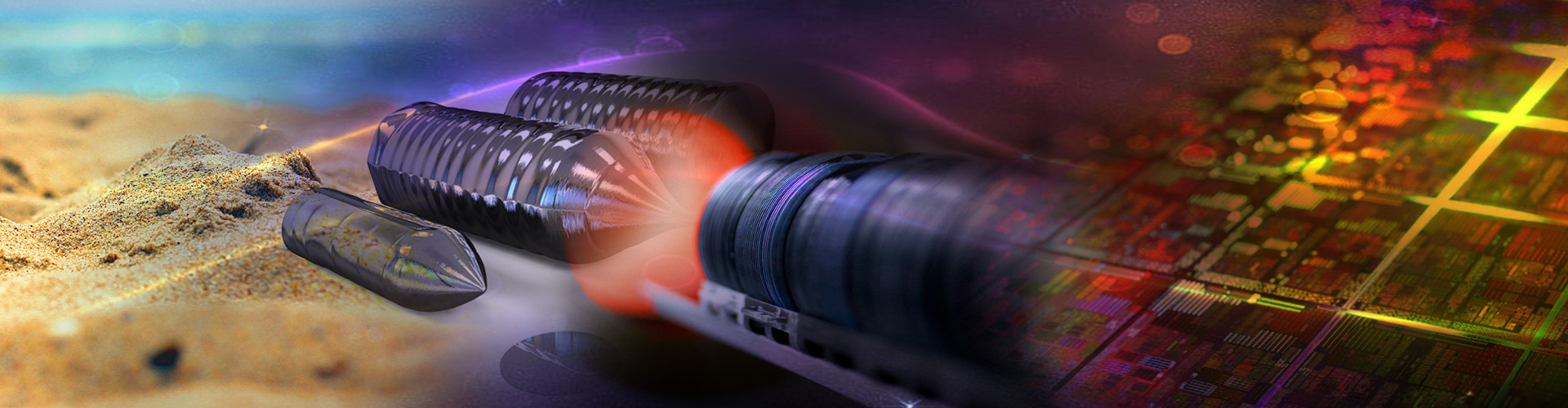
Ultra-high temperature tube furnaces up to 2200°C
Electron’s hot-wall furnace for SiC wafer processing offers excellent temperature uniformity, fast heating & cooling rates and scale at ultra-high temperatures.
Why choose for Electron?
In-depth process knowledge
We know the challenges that arise when renewing and/or replacing existing installations as well as scaling up laboratory setups to fully-fledged production. And we provide the expertise needed to streamline this. We are not just a supplier; we are your knowledge partner, focused on smoothly guiding businesses through this process.
Our in-depth process knowledge goes beyond just technical aspects; it also includes the strategic decisions essential for a successful scale-up. Process development is essential in the journey to large-scale production. Our experienced engineers are here to provide support in both analyses and performing tests.
Electron has in-house R&D facilities for process validation. This offers a unique opportunity to test production runs on a scale comparable to a production machine.
Consistent performance and built-in verification
In a world where precision is essential, our systems stand out by achieving exceptional temperature and flow uniformity, even with a full load. Built-in verification capabilities and extensive data logging help to document executed processes. This also ensures that our installations comply with the latest AMS2750 guidelines.
Safety in UHT SiC wafer processing
In SiC wafer processing, working with complex and reactive materials requires the highest level of safety. Our UHT furnaces meet the highest safety standard. Specifically designed to handle complex substances, these furnaces ensure secure operations essential for SiC processing.
Ultra-high temperature furnaces for SiC wafer processing. UHT tube furnaces up to 2200°C. Our hot-wall furnace design ensures optimal performance.